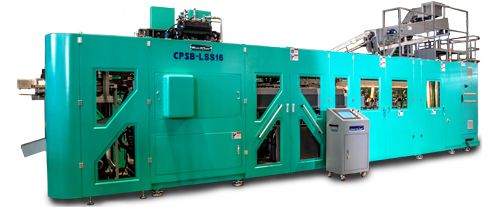
As the leading high-speed PET SBM manufacture in Taiwan, Chumpower has constantly pushing the limit of linear machine. Now, for the first time, Chumpower’s newest 16 cavities linear machine has broken the 20,000 BPH barriers and into the region where once was considered only achievable by rotary blow molding machine.
The LSS16 stretch blower is a fully electric machine driven by ten servo motors, from the heavy-duty clamping system to fast-responding sealer or preform-eject actuation, precise servo synchronization and high mold cavity count are the two key factors making high output capacity possible.
The eight cavities machines are one of the best-selling models from Chumpower. This platform has been well-tested within the industry for years, thus is the most suitable candidate for Chumpower to design the LSS16 based on that platform. Since this new model has nearly the twice production capacity, robust clamping and fast-responding subsystems were essential in making the new machine stable during production.
The clamping system was driven by two servo motors actuating each side of mold, since the mold has long horizontal span to house sixteen 500cc bottles, strong cam-driven indexer were used to transfer the high torque from servo motor to the swing arm and push-rod system which subsequently also drive another cam to actuate the base mold . Two sets of servo motors drive the stretching system via rack-and-pinion mechanism. Also sealers were servo driven actuated by cams.
Ten modules of heating ovens were fitted on the machine to heat 24,000 preforms per hour, and Chumpower’s narrow pitched preform chain (38mm) allows more preforms to be heated at one time. Each oven is controlled by advanced IR heating-control system from Olicorp to regulate the electrical current and ensure stable IR lamp output. The estimated average power consumption of the LSS16 for producing a single bottle would be 1.9 Watts. The fluid-dynamics for heating ovens and reflectors were also studied during the design stage to ensure optimum heating environment is maintained for the preforms while allowing other components to stay within the targeted temperature range.
The LSS16 is the first machine from Chumpower to feature the quick change sealer design, and since the mold change and stretch rod setting are relatively straight forward, thus helps in shortening the production change-over period.
Recovery system is standard for this machine, featuring European based blow valve system with fast responding time and low dead space volume. This system was also well tested within the industry. The estimated air consumption rate for producing 600cc bottles with 11.5 grams preforms at 24,000 BPH is 16.8 m ³/min, and the total energy consumption rate is 45.6 kWh.
The most important aspect for Chumpower to create this high output machine is to offer our client the possibility to couple the blowing machine to high-output rotary filler and formed a combi system, which illuminate the need for expensive air conveyors and saves precious floor space. By linking the LSS16 to bottle-handler system, the finishing bottles are precisely carried from the blower and feed into the star wheel of the filler. CCD camera system can also be installed in the downstream conveyor belt to monitor the output bottle from the combi system for proper filling level and closure capping.
Traditional combi line uses a rotary blow molding machine as the blower, however, this setup would poses a higher entry barrier for new comers in the PET bottle industry. Therefore Chumpower’s combi system concept or the LSS16 machine is very suitable for client who is looking to setup a medium to high production capacity line.